Features of booking PVC boats
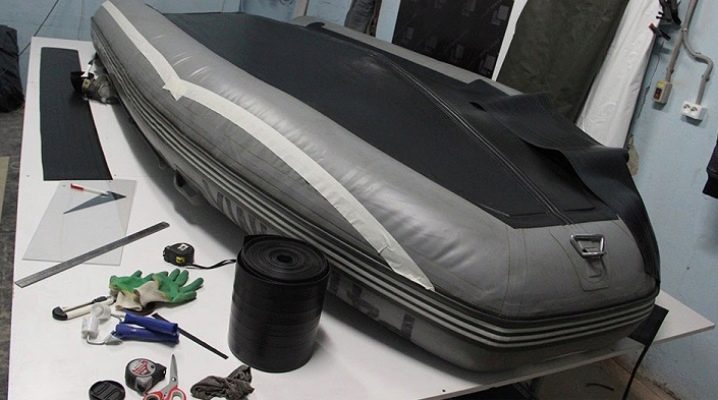
An inflatable rubber boat, or made of polyvinyl chloride, is a fairly light and comfortable solution for small size watercraft. Such boats are in great demand among anglers and travelers. The main problem in use is damage to the bottom and cylinders - ruptures, punctures and other damage. To strengthen the bottom, various methods are practiced, for example, booking a swimming facility.
This publication will allow you to find out what booking methods are available, what materials are used, their pros and cons, and also how to do it yourself.
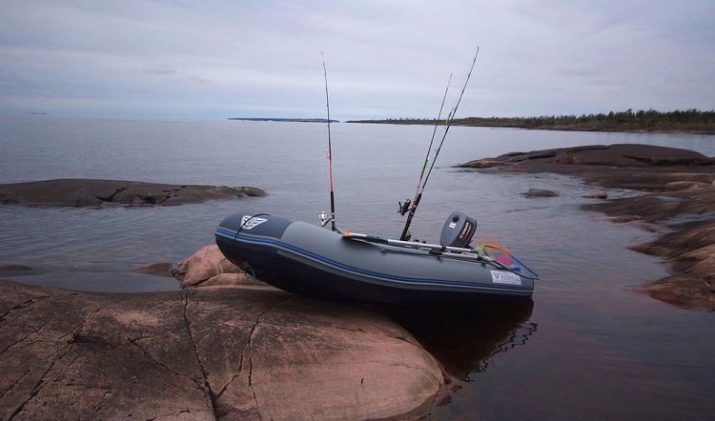
Description of the procedure
There are many factors that cause damage to the bottom of the craft, as well as its cylinders and other elements, for example:
- wear of the material, its abrasion;
- rupture when the bottom and bottom of the cylinders come into contact with the rocky soil of the reservoir, pebbles, and so on;
- breakdown or cut with a pointed object (dropped a knife, hooked a fishing rod and more);
- got a spark on board.
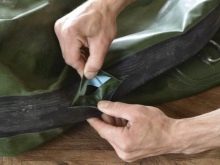
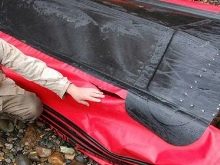
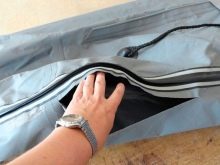
You can simply sit on an inflatable board when the boat is in the shallows, and get a breakdown or rupture of the lower part of the skin.Similarly, when pulled ashore, careless dragging over the pebbles can provoke damage to the PVC layer. As you can see, there are many factors, and they are very heterogeneous.
A way to resolve trouble can be an event such as armoring of the lower part of the boat made of polyvinyl chloride, strengthening and thickening of the bottom and inflatable sides. At the moment, many methods have been invented, using which you can free yourself from such problems for a long time.
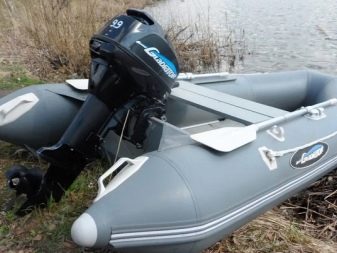
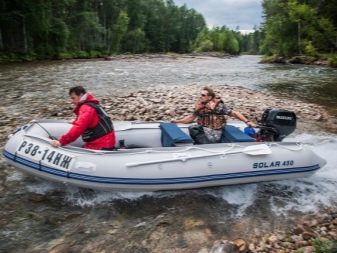
The main thing in the implementation of all measures to strengthen it is necessary to take into account the following nuances:
- the mass of the watercraft, which can grow up to 7-12 kilograms, it all depends on the dimensions of the watercraft and the patch;
- it is worth remembering that as a result of gluing polyvinyl chloride, the dimensions will increase by 2-3 centimeters;
- what material will be used for booking (since the boat is made of PVC, it is also necessary to make an additional bottom from PVC tapes or specialized rubber-coated strips, however, anglers often use other, waterproof materials);
- the thickness of the glued polyvinyl chloride should be in the range of 3-5 millimeters;
- what areas of the bottom are armored (this depends on what the reinforcement is for).
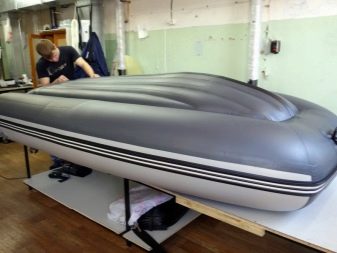
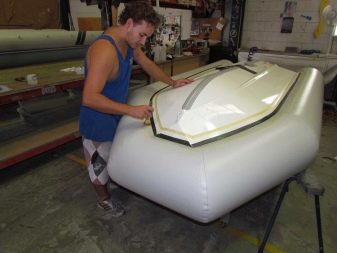
However, it's basically:
- inflatable keel;
- the lower part of the cylinders;
- bow of the craft;
- place of fixation of the transom;
- areas of conjugation of longitudinal stiffeners (stringers) in the cockpit.
It should be taken into account that strengthening the center strip and torpedoes will bring negligible protection and light stability. But with a major reservation of the bottom or even the entire watercraft, you can definitely be sure of the boat.
The main thing is to use the appropriate glue. In addition to all underbody protections, an auxiliary reinforcement can be made.
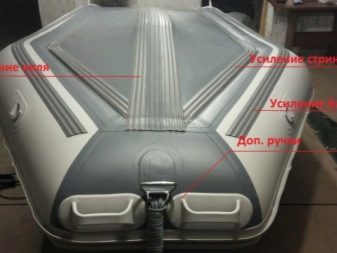
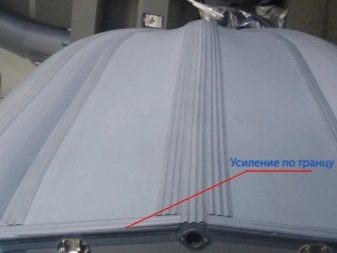
What will be required?
There are several methods of strengthening, each of them has its own positive qualities and shortcomings. Armoring can be used for the entire bottom of the PVC inflatable floatation, or only areas that are most at risk of wear or damage can be armored. Key methods include:
- sticking to the bottom of the scales of polyvinyl chloride ("dragon skin");
- additional protective coating of polyvinyl chloride on the lower part;
- strengthening with polyurethane film;
- PVC tape;
- rubber coated tape;
- liquid polymers.
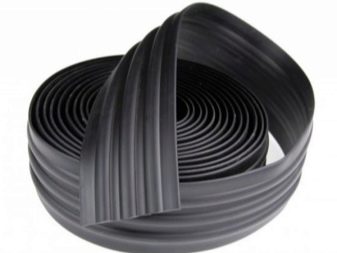
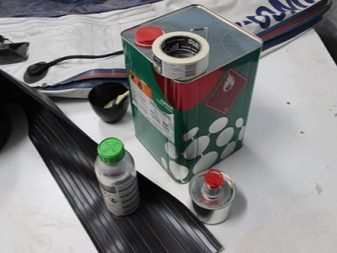
Sticking "dragon scales" is a long-term and labor-intensive procedure, not everyone wants to spend time on such an operation. An additional layer of PVC is not so ingenious and long-term process, and PVC tape, glued to strengthen and armor on elements that are subject to maximum loads, such as the bottom of a boat, will be the most ingenious and cost-effective solution, significantly reduce costs. It is equally possible to use a rubber-coated tape for this purpose, using a specialized adhesive. Separately, it is necessary to disassemble application of liquid polymeric materials.
The polymer liquid is applied to the pre-prepared area of the boat. Certain varieties of it are practiced for deep armoring of a boat.In addition, fishermen perform reinforcement with strips of plastic, aluminum or duralumin, putting them on rivets in the middle, in front or at the stern of the craft. This method is not good enough in that it harms PVC by abrading it. And it interferes with the normal assembly of the boat. In general, armor can be made on any part of the boat by various methods, to what extent there is enough knowledge and fiction.
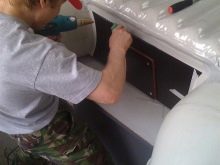
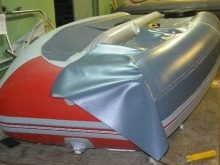
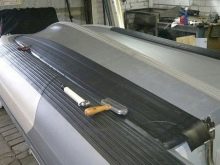
Strengthening pros and cons
The process of booking the bottom of a swimming facility brings a number of positive aspects, in the aggregate, the funds spent are not wasted, but turn into a profitable investment. This procedure does the following:
- increasing the strength of the bottom and reducing the possibility of breaks and punctures;
- an increase in the service life of the product, as resistance to wear, the influence of the atmosphere, and so on is enhanced;
- the watercraft receives the property of better gliding, which affects the running characteristics;
- the cost of the boat increases, it can be sold at a higher price.
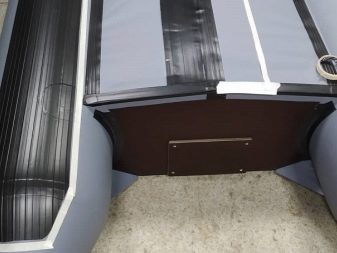
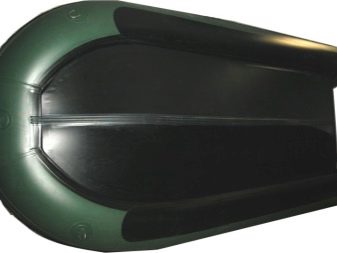
If we talk about negative points, then from among them we can touch a certain increase in mass, its value depends on the dimensional parameters of the craft and the thickness of the used protective layer on the bottom. Additionally, this indicator is influenced by the material used for booking. After refinement, the dimensions will increase slightly, but also not too noticeably, within the limits of 2 to 3 centimeters.
According to the current opinion among fishermen and travelers, such minor inconveniences will be fully compensated by increasing the duration of operation and improving driving properties, and the use of the latest polymeric materials makes it possible to exclude an impressive increase in the weight and size of the boat.
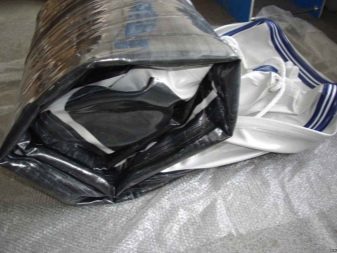

Application of liquid polymers
Modern science has given life to the so-called elastic polymers - liquid chemicals that are able to polymerize after coating the surface of a floating craft. Polymerization gives extraordinary strength, such a coating will not lag behind under any influences.
Polymers combine qualities that were previously incompatible in one substance - good elasticity and stability to the influence of mechanical factors. Such features are acquired during the manufacturing process through the introduction of specialized additives and plasticizers that affect the physical and chemical characteristics of the finished product.
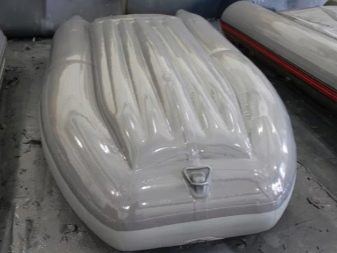
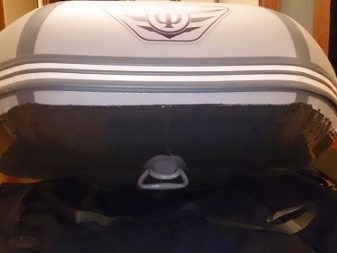
Due to the coating of the surface of the craft with liquid polymers, it acquires the following qualities:
- resistance to the influence of mechanical factors (wear, cuts, holes, etc.);
- resistance to the influence of chemical aggressive substances;
- significant resistance to UV radiation;
- increased weather resistance, especially to temperature fluctuations.
It should be said that the applied polymer layer stands out among other types of coatings by its thinness, its thickness is not more than 0.8 millimeters, and its density is close to the density of the material of the floating facility. All this makes it possible to reduce the amount of mass added after coating to the maximum.If necessary or desired, coating with several layers of polymer is allowed.
Such compounds can be purchased at specialized outlets, and their use does not require special knowledge and skills.
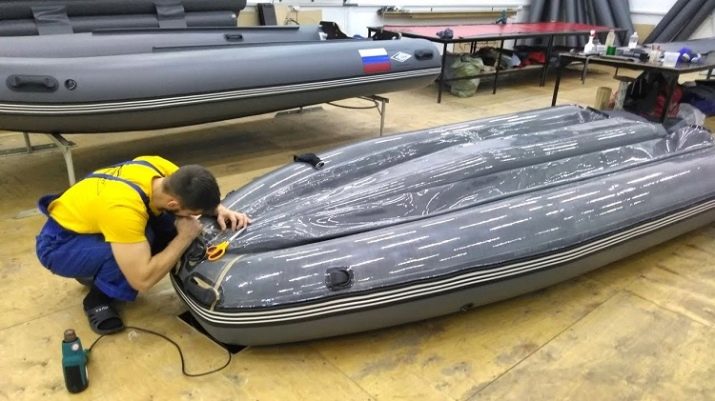
detailed instructions
First of all, it is required to strengthen the structure. Taking into account the reliability of the supporting structure, armor is required only for the bottom of the craft and inflatable sides. This can be done in two ways. Only after the completion of this process will it be possible to talk about other types of reconstruction. Although the PVC boat is made of a fairly strong material, there is nowhere to hide from wear, and for this purpose, specialized PVC profiles are used, which are fixed with or without waterproof glue.
As a result, as already mentioned, the mass of the floating facility will slightly increase, therefore, such a procedure should be carried out, taking into account the following recommendations:
- booking in any case is necessary when operating a watercraft in a fast current with rapid sections of the river, in such conditions there is a particularly high risk of damage;
- when operating a watercraft on ponds and lakes with still water, this can be omitted.
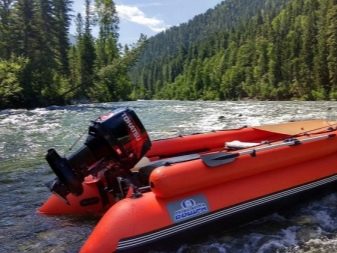
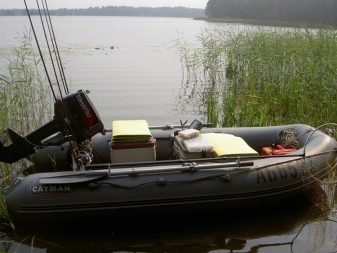
Membrane armor
The procedure goes as follows:
- before proceeding with the main activities, the boat must be thoroughly washed, dried, all small grains of sand removed and degreased with a solvent;
- after that, it is pumped up in order to make a template for cutting material, for this it is turned upside down and measurements are taken from the keel to the cylinders;
- then, according to these measurements, the material is cut out (it is desirable to prepare two identical strips) and left in the sun or removed in a warm place so that it evens out;
- then the boat is blown off by pulling out the valve, laid out on level ground;
- one strip is attached to the bottom, leveled along its entire length, and they begin to heat it with an industrial hot air gun set to the limit mode, rolling it in parallel with a roller in order to remove air;
- then exactly the same actions are performed with the 2nd strip, precisely attaching it to the first.
The bonding procedure is carried out by heating the membrane by exposing it to an elevated temperature. No glue is required.
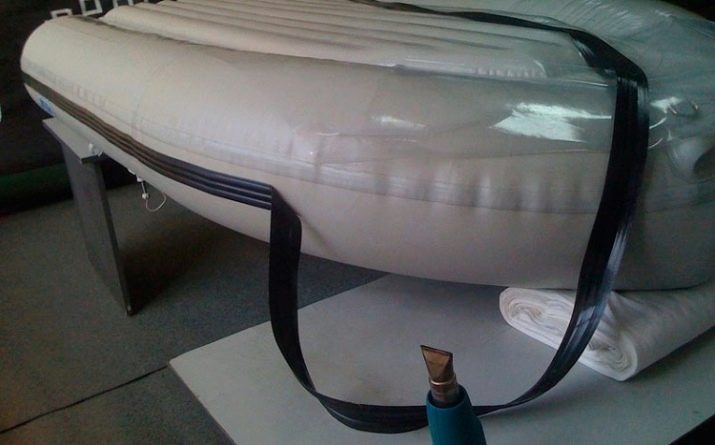
Reservation of cylinders with a halt
The second component of the craft, which needs additional reinforcement, is the cylinders, or rather, the part of them that is in the water. There is no need to completely veneer them with material. The procedure is carried out in exactly the same way as when booking the bottom: the cylinders are initially cleaned, the air is driven off, the dimensions are taken and the material is glued.
Additionally, halts are used for booking - glued to the bottom area of the cylinders. Halts are sold at specialized outlets where you can choose the material for specific modifications of boats. In a situation where there are no halts for your model, you can buy for a different modification and use it for your watercraft after adjusting it to your size.
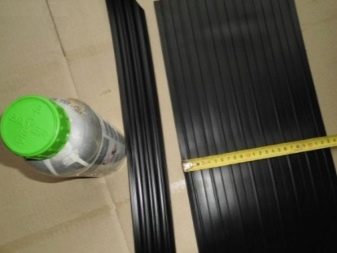

The halt booking procedure includes the following steps:
- as in the process of booking the bottom, everything is cleaned and dried, but gluing in this case is carried out exclusively on an inflated boat;
- after it needs to be cleaned with a solvent and left for some time to dry;
- then glue is applied to the cylinders and the halt, held for 10 minutes and the halt is applied to the lower region of the cylinder, after which it is also required to roll it with a roller to remove air, level and compact.
Drying is usually 2 or 3 days.
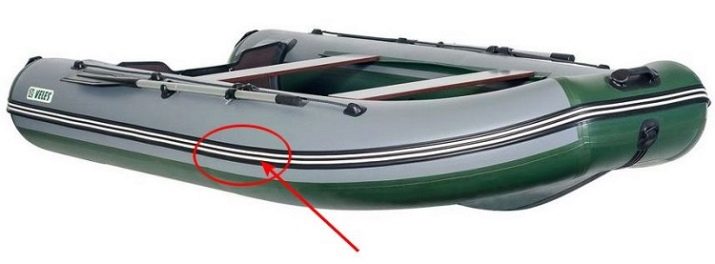
How to stick a protective tape to the bottom of the boat, see the following video.